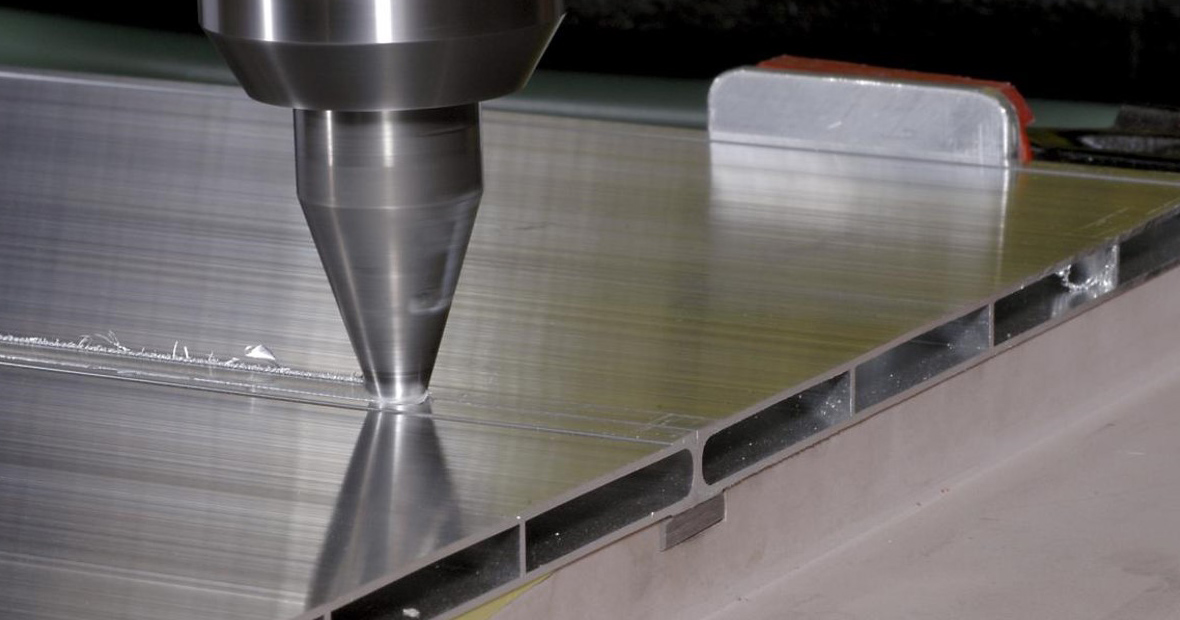
Friction stir welding, a solid-state joining process, has become a revolutionary method for combining aluminum alloys. This innovative technique offers numerous benefits including heightened joint strength, durability, and superior weld aesthetics, while reducing the need for extensive post-weld finishing. Furthermore, this process involves significantly less heat input, thereby preserving the material's original integrity. Of course, the quality of a friction stir weld isn't solely dependent on the process itself, but also largely influenced by factors like tool rotation speed, welding velocity, and the tool pin's profile. Each of these elements plays a pivotal role in determining weld strength, joint homogeneity, grain size, material flow, and overall mechanical properties. Moreover, friction stir welding induces dynamic microstructural transformations within aluminum alloys, a fascinating phenomenon warranting closer examination. Finally, to assess the comparative impact of this welding technique, a meticulous study of mechanical properties between welded and base material is warranted.
Exploring the advantages of friction stir welding in aluminum alloys
Delving into the realm of engineering and metalworking, friction stir welding (FSW) presents a promising technique for enhancing the structural resilience of aluminum alloys. This process, known for its benefits in mitigating welding defects, has a considerable impact on the quality and uniformity of the welded zone. One of the distinguishing aspects of FSW lies in the controlled rotational speed of the tool used, which contributes significantly to the weld quality.
Enhancing Joint Strength and Durability in Aluminum Welds
Aluminum alloys, when subjected to FSW, exhibit enhanced joint strength and durability. This observed improvement is largely attributed to the unique process of FSW, which facilitates a more even heat distribution, thus reducing the distortion of aluminum alloy parts.
Minimizing Heat Input : Preserving the Aluminum Alloy's Integrity
FSW has been found to preserve the integrity of aluminum alloys by minimizing heat input. This is achieved through a precise thermal control, which optimizes the microstructure of the aluminum alloys.
Improving Weld Appearance and Reducing Post-Welding Finishing Needs
Another advantage of FSW in aluminum alloys is the improved weld appearance, significantly reducing the need for post-welding finishing. This benefit is tied to the selection of the appropriate tool, a factor of paramount importance to maximize the advantages of FSW in aluminum alloys.
Key parameters influencing the quality of fsw joints in aluminum
Understanding the process of friction stir welding (FSW) is key in ensuring the outcome of a smooth, strong, and high-quality weld. The fusion of aluminum alloys relies heavily on several parameters that govern the FSW process. One of these parameters that significantly impacts the quality of FSW joints is the tool rotation speed. A higher rotational speed while welding can enhance the strength and alter the microstructure of the welds, providing a uniform and defect-free joint.
The Impact of Tool Rotation Speed on Weld Strength and Microstructure
Tool rotation speed directly influences the heat generation and the material flow during the FSW process. The correct rotational speed can result in a homogeneous and strong FSW joint in aluminum alloys.
The Role of Welding Speed in Determining Joint Homogeneity and Grain Size
Welding speed, another vital parameter, plays a crucial role in achieving joint homogeneity and controlling grain size. A slower speed typically results in a finer grain structure, enhancing the mechanical properties of the joint.
The Effect of Tool Pin Profile on Material Flow and Mechanical Properties
The tool pin profile is another determining factor for the quality of FSW joints. Different pin profiles affect the material flow during FSW, thereby influencing the mechanical properties of the joint. The right tool pin profile can ensure a defect-free and strong weld.
Other parameters, including the direction of welding and the choice of tool material, equally contribute to the quality of Fsw welding. The direction of welding influences the distribution of particles within the joint, while the choice of tool material impacts the temperature generated during welding, ultimately affecting the quality of the weld.
Microstructural transformations in aluminum alloys due to fsw
One of the most fascinating aspects of friction stir welding (FSW) in aluminum alloys is the microstructural transformations that occur. Grain size variations in the weld zone significantly impact the mechanical properties of aluminum alloys. During the FSW process, secondary phase dissolution and precipitation in aluminum alloys are influenced in a unique manner. This results in the formation of specific textures in the microstructure, observed in the examined samples of aluminum alloys.
Another noteworthy aspect of the FSW process is the effect of the FSW tool's rotation speed on the microstructure's heterogeneity in the heat-affected zones. This aspect plays a significant role in determining the material's final properties. On the other hand, microstructural defect mechanisms like porosities or cracks are a common concern in FSW of aluminum alloys. However, with proper understanding and control of the process, these can be prevented, enhancing the integrity of the material's surface.
Through comparative analysis of the aluminum alloy microstructure before and after FSW, significant insights into the microstructural transformations are gained. This underlines the potential of FSW as a promising technique for joining aluminum alloys, providing a deeper understanding of the process and the materials involved.
Comparative study of mechanical properties in welded and base material
Friction stir welding of aluminum alloys offers an intriguing perspective into the realm of materials engineering. The
reveals intriguing contrasts and parallels. In-depth analysis of distinct mechanical properties in base and welded materials uncovers fascinating technical details. A stark contrast exists for instance, between the tensile strength measured in Mpa of the base material and that of the welded joint. The weld, often made from dissimilar materials, can exhibit different hardness or microhardness levels.
Each welding method has a distinct influence on the final material's mechanical properties. The strength and durability of structures, whether in the construction, automotive, or aerospace fields, is significantly impacted by the choice between base and welded materials. Noteworthy is the role of advanced welding technologies that potentially enhance the mechanical properties of welded materials. An understanding of the latest research and discoveries in this domain helps in making informed decisions. Additionally, safety standards and regulations pertaining to the use of base and welded materials need to be a prime consideration.
Real case studies provide valuable insights into the significant impact of the choice between welded or base materials on project outcomes. Equally essential is the understanding of the environmental implications and the costs associated with the use of welded materials compared to base materials. These costs include production, maintenance, and replacement expenses. The fracture of the alloy, whether it's aluminium or other materials, can be a determining factor in this comparative study of base and welded materials.