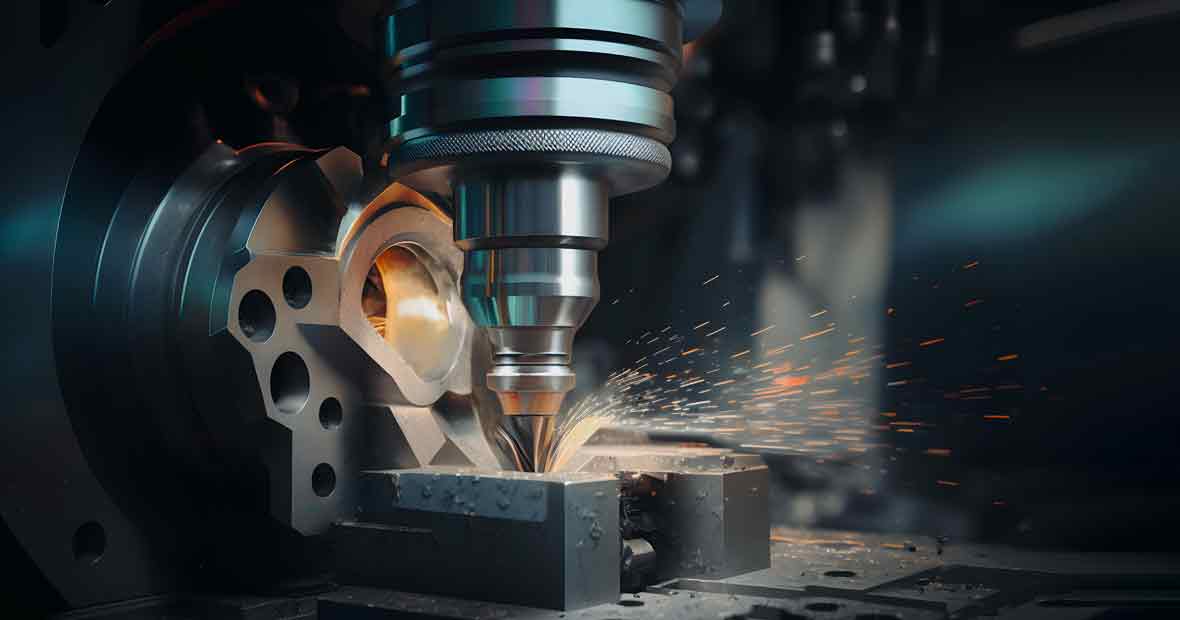
The intricate relationship between mankind and technology has always revolved around the creation, modification, and application of tools. Cutting technology, in particular, is a pillar of this bond, tracing its roots to the earliest human civilizations that crafted sharp-edged tools from stone. Throughout centuries, it has transformed, expanded, and refined, becoming pivotal to an array of industries. Today, industries from automotive to aerospace, construction to manufacturing, rely heavily on cutting technology for precision, efficiency, and automation in their production processes. Its significance is such that the evolution of cutting technology often mirrors the broader progress of industrial development.
Historical Development of Cutting Machines
To appreciate the present state and anticipate the future trajectory of industrial cutting machines, it's essential to understand their past – a journey that is as much about human innovation as it is about technological advancement.
Early Methods and Tools
The history of cutting technology begins with humanity's earliest tool-makers, who sharpened stones and bones to meet basic survival needs. Over millennia, as societies began to cultivate the earth, build structures, and forge weapons, cutting tools evolved concurrently. Metalworking ushered in a new era of cutting, with bronze, iron, and later steel tools marking significant leaps in efficiency and versatility.
Industrial Revolution: The Birth of Cutting Machines
The Industrial Revolution was a turning point for cutting technology, aligning with the rising demand for mass production. The invention of cutting machines mechanized previously manual processes, propelling industries like textile, steel, and manufacturing into unprecedented productivity levels. This period saw the introduction of the band saw, milling machines, and the turret lathe, among other devices – each contributing to faster, more consistent, and scalable cutting processes.
20th Century Innovations: Automation and Precision
With the advent of electricity and subsequently computer technology in the 20th century, cutting machines experienced another transformative shift. The focus was on automation, precision, and complexity. Numerical control (NC) machines appeared during the mid-century, and by the 1970s, Computer Numerical Control (CNC) machines emerged, bringing about increased precision and efficiency. Later, technologies like laser and plasma cutting further expanded the capabilities of cutting machines, allowing for cutting at higher speeds, greater thickness, and intricate shapes.
Current State of Industrial Cutting Machines
Fast forward to the present, industrial-cutting-machine.com's industrial cutting machines have advanced tremendously, not only in terms of technology but also in their diversity, complexity, and applications across different industries.
Types of Cutting Machines
There's a myriad of cutting machines available today, each offering distinct advantages depending on the application. Among the most common are laser cutters, plasma cutters, waterjet cutters, and CNC machines, each specialized for certain materials and precision levels.
Laser Cutting Machines
Laser cutting machines use a high-powered laser beam to cut through materials. They offer high precision, speed, and the ability to cut complex shapes. They are widely used in industries such as automotive, aerospace, and electronics, where precision is paramount.
Plasma Cutting Machines
Plasma cutters utilize a high-velocity stream of ionized gas, or plasma, to cut through conductive materials like steel and aluminum. They provide high cutting speeds, can handle thick materials, and are often used in heavy-duty industrial applications.
Water Jet Cutting Machines
Water jet cutting machines employ a high-pressure stream of water, sometimes mixed with abrasives, to cut materials. They are versatile and can handle a broad range of materials, including metal, glass, stone, and composites, without generating heat, thereby reducing the risk of material distortion.
CNC Cutting Machines
CNC machines represent the integration of computer technology with mechanical cutting. They offer high precision, consistency, and flexibility, being able to produce a wide variety of shapes and designs based on digital instructions. They find applications in a vast array of industries, from woodworking to metal fabrication and beyond.
Applications in Various Industries
Modern cutting machines cater to various industry needs. In construction, they assist in shaping building materials; in the automotive and aerospace industries, they aid in creating intricate parts; in textiles, they contribute to fabric cutting with precision; and in electronics, they help in the manufacture of tiny and intricate components. The list is vast, illustrating the ubiquity and necessity of cutting technology in today's industrial landscape.
Technological Advances in Cutting Machines
The evolution of cutting machines continues unabated, fueled by technological advancements across various fronts.
Automation and Robotics
Automation and robotics have become increasingly prominent in the cutting technology sphere. Automation improves efficiency, reduces human error, and can lead to significant cost savings. Meanwhile, the use of robotics provides flexibility and precision, especially in executing complex cuts and handling delicate materials.
Software Integration and Optimization
As digital technology progresses, software integration plays a vital role in enhancing the performance of cutting machines. From CAD/CAM systems for design and manufacturing to advanced algorithms for optimizing cutting paths and predicting machine maintenance, software is integral to modern cutting technology.
Materials and Durability Enhancements
As the materials to be cut diversify and their properties evolve, so must the cutting machines. Therefore, advancements in materials science greatly influence the evolution of cutting tools. The focus is on developing cutting heads and blades with enhanced durability, capable of handling tougher, more resilient materials.
Energy Efficiency and Sustainability
With growing concerns over environmental impact and sustainability, energy efficiency has become a key consideration in the development of cutting machines. Innovations are geared towards reducing power consumption, utilizing renewable energy sources, and minimizing waste generation.
Challenges and Solutions
While the progress in cutting technology is impressive, it is not without challenges, ranging from operational issues to safety concerns and environmental impact.
Operational Challenges
As cutting machines become more complex, maintaining them can prove challenging. They require skilled personnel for operation and maintenance, and breakdowns can lead to significant production downtime. Moreover, the integration of software and hardware introduces the risk of cybersecurity breaches.
Safety Concerns
The operation of cutting machines involves inherent risks, from the handling of sharp and hot materials to the emission of potentially harmful gases. Ensuring the safety of operators and the work environment is thus a paramount concern.
Environmental Impact and Regulations
The environmental impact of cutting operations, particularly in terms of energy use, waste generation, and emissions, is a significant challenge. This is further compounded by stringent regulations aiming to curb industrial environmental footprints.
Solutions and Best Practices
Solutions to these challenges lie in technological innovation, training, and adherence to safety standards. For operational challenges, predictive maintenance, AI-driven quality control, and robust cybersecurity measures can offer substantial improvements. Safety can be enhanced through proper training, use of protective equipment, and design of machines with safety features. To address environmental concerns, adoption of energy-efficient technologies, waste recycling, and the use of eco-friendly materials are among the best practices being pursued.
Future Trends: Cutting Technology in the Coming Decades
Looking ahead, cutting technology is poised for further transformation, underpinned by emerging technologies and industry trends.
Emerging Technologies
Emerging technologies like artificial intelligence, machine learning, and IoT are set to reshape cutting technology. They promise to bring about smarter, autonomous cutting machines capable of self-optimization and adaptive learning, enhancing productivity and efficiency further.
Integration with Industry 4.0
As the Fourth Industrial Revolution, or Industry 4.0, takes hold, cutting machines will increasingly be integrated into digitalized, interconnected production ecosystems. This involves the convergence of cyber-physical systems, the Internet of Things, and cloud computing.
Customization and On-Demand Production
The future of cutting technology also aligns with the broader shift towards customization and on-demand production. With flexible and quick-to-configure cutting machines, manufacturers can efficiently cater to individualized product demands, accelerating the shift from mass production to mass customization.
Global Market Dynamics
Lastly, global market dynamics will influence the evolution of cutting technology. Factors like the growing manufacturing sector in developing economies, increased investment in automation technologies, and the shifting regulatory landscape will shape the development, deployment, and adoption of advanced cutting machines.