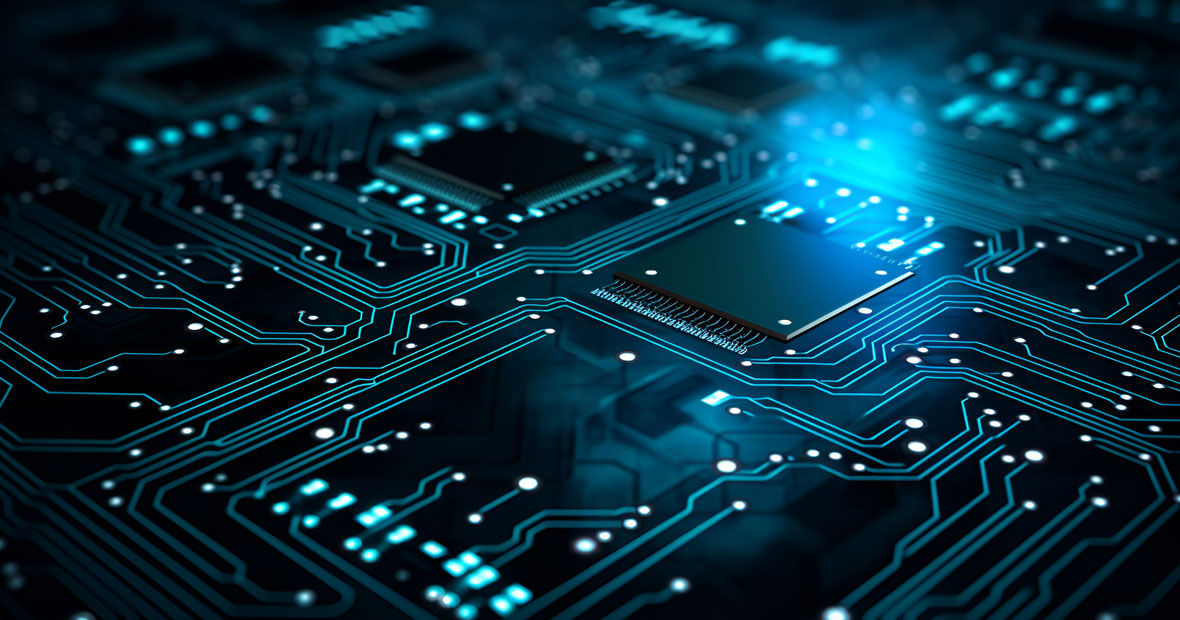
As the world of electronics continuously evolves, the pressure to maintain pace with the rapid progression of technology is ever-pressing. Central to this technological revolution is the development of Microvias PCB technology, a groundbreaking innovation that is reshaping the landscape of electronic devices. This technology, characterized by its efficiency and miniaturization, redefines the conventional norms of drilling techniques. Pioneering a shift from the traditional mechanical process to sophisticated laser drilling, Microvias has ushered in an era of precision and speed unparalleled in the industry. This advancement is not mere progression; it is a seismic shift that holds profound implications for High-Density Interconnect (HDI) boards and their role in contemporary electronics.
Advancements in drilling techniques: from mechanical to laser drilling
Within the domain of electronic devices, the manufacturing process of microvias printed circuit boards (PCBs) has experienced significant evolution. This transformation, from traditional mechanical drilling to advanced laser drilling, marks a leap in technology. The role of these advancements in laser drilling has been pivotal in the miniaturization of PCBs, leading to more efficient, compact, and powerful electronic devices. Corresponding to the progress in the drilling process is the reduction in production costs, making the manufacturing of PCBs more economical.
Evolution of Drilling Technology for Precise Microvia Creation
Drilling technology has evolved significantly over the years, with the transition from mechanical to laser drilling constituting a major milestone. This swift change has been driven primarily by the demand for smaller, more precise microvias by microvias pcb manufacturer.
Benefits of Laser Drilling : Accuracy, Speed, and Versatility
Laser drilling offers numerous benefits such as precision, swiftness, and adaptability. In comparison to mechanical process, laser technology provides better quality and a high level of accuracy, which is essential in PCB manufacturing.
Comparing Mechanical and Laser Drilling in PCB Manufacturing Efficiency
While both mechanical and laser drilling have their pros and cons, the latter has proven to be more efficient in terms of precision, quality, and cost-effectiveness. The implementation of laser drilling for microvias, however, has its share of challenges and solutions. Looking forward, the future of drilling in the PCB industry is expected to be shaped by innovations and emerging trends in laser technology.
Microvias pcb technology: a key enabler for hdi boards in modern electronics
Advancements in Microvias PCB technology have propelled the evolution from traditional design to cutting-edge High-Density Interconnect (HDI) technology. Microvias, tiny holes drilled by lasers, are significant in reducing the size and boosting the functionality of PCBs. By allowing more components to fit in a smaller space, they enhance the electrical performance of electronic devices, proving to be revolutionizing agents in the electronics industry.
Manufacturing HDI PCBs pose specific challenges, yet microvias offer feasible solutions. Techniques to create microvias, such as laser drilling, have overcome issues related to space constraints and complex circuit patterns. This has facilitated the production of denser and more efficient PCBs, highlighting the pivotal role of microvias.
As devices continue to shrink in size, microvias have become a crucial factor in electronics' future. The miniaturization trend in electronics is far from slowing down, with increasingly smaller and more powerful devices becoming the norm. In this scenario, microvias in PCBs are more significant than ever, ensuring optimal functionality within compact electronic devices.
The impact of microvias on signal integrity and electrical performance
Advancements in modern technology, particularly in the realm of electronics, owe an immense credit to the evolution of printed circuit boards (PCBs). A significant aspect of this evolution is the introduction of microvias, small holes drilled by lasers that serve as electrical connections between layers in a multilayer PCB. Microvias have been instrumental in driving efficiency and miniaturization of electronic devices.
One of the notable benefits of microvias is the enhancement of signal integrity. By reducing electrical distances, microvias help maintain the strength and clarity of the signal across the PCB. This effect correlates with improved electrical performance, including a decrease in crosstalk and an improvement in frequency response.
Microvias play a critical role in optimizing the impedance of PCBs, which in turn greatly bolsters performance. Optimized impedance ensures a smooth flow of signals, reducing the likelihood of signal errors and thereby enhancing the reliability of electronic devices.
However, the use of microvias in PCBs also presents a challenge in terms of thermal management. Solutions for this issue often revolve around proper design and placement of microvias to ensure adequate heat dissipation.
Material innovations and their contributions to reliable microvias pcb manufacturing
The evolution of copper alloys has contributed significantly to improved conductivity within microvias, enhancing the efficiency of PCB manufacturing. This advancement in material composition has facilitated a marked improvement in signal transmission across various electronic devices. Additionally, the progression in epoxy resins and other polymers has played a role in augmenting the thermal stability of PCBs, ensuring a robust and durable build quality.
Equally noteworthy is the influence of nanomaterials in reducing the size and elevating the reliability of microvias. The incorporation of these microscopic materials into the manufacturing process has revolutionized the field, allowing for the production of smaller, more efficient microvias. Innovations in dielectric materials have further bolstered the insulation and performance of microvias, delivering superior electrical properties and improving overall device performance.
Shifting focus to the manufacturing process, the role of advanced copper deposition techniques in the precise fabrication of microvias cannot be understated. These cutting-edge methods have fine-tuned the manufacturing process, boosting its precision and reliability. Lastly, the introduction of recyclable materials into microvias production has paved the way for a more sustainable manufacturing process, aligning with global sustainability goals and ensuring a greener future.